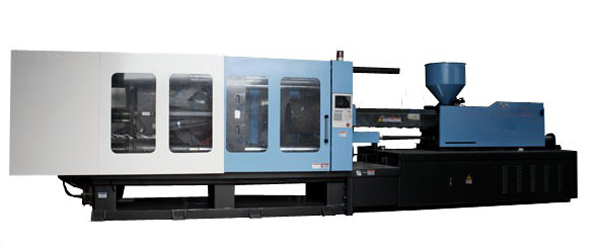
Features:
Clamping Unit 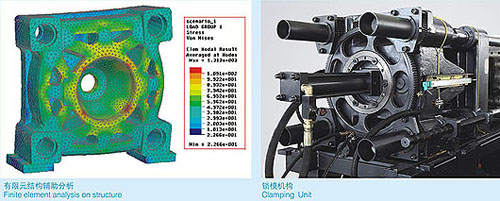
·Five
pivots hyperbolic toggle clamping mechanism has characteristics with fast
opening and closing, stable and energy saving through the optimized design.
·With Differential high speed mould locking function, it can effectively
shorten the molding cycle time and improve the work efficiency of the machine.
·The mould plate adopts the finite element technology on structure auxiliary
analysis, that makes the mould plate structure more reasonable, strength and
resistance to fatigue better, extending service life;
·High rigidity ant fraying tie bars plated with hard chromium has advantages of
high precision, high strength, high strength and long life.
·Reliable low pressure protection function greatly prolongs the service life of
the mould.
·The clamping and ejecting stroke of the mould are controlled by high precision
electronic sensor, the setting precision can achieve + / - 0.1 mm. Low pressure
protection and ejector stroke set get more directly and simply.
·The protection devices of mechanical, hydraulic and electrical ensure that the
operating personnel is safety, and fully embody enterprise culture with
human-oriented. (Note: Size above BJ400 machine, the hydraulic safety
protection device is the standard configuration.)
·To control lubrication system automatically according to how many times to
open and close the mould, the automatic quantitative lubrication system can
guarantee the clamping machine more stable, reliable, and longer life.
·Hydraulic motor with gear adjustable system, makes mold adjustment more
reasonable and perfect.
Injection Unit 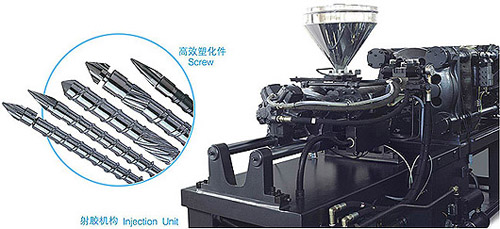
·High efficient separation type screw, high mixing screw and all
kinds of special screws improve the applicable scope of the material and
guarantee molten material uniform and measurement stability.
·Duplex balanced injecting device provides higher injection pressure, makes the
unit more simple and stable, and lowers the failure rate. It is more convenient
to maintain and save space meanwhile.
·Machines above BJ288 with double injection shift cylinder accept the stress
more reasonable and effectively prevent the nozzle deviation, avoid material
leakage.
Features of
hydraulic system 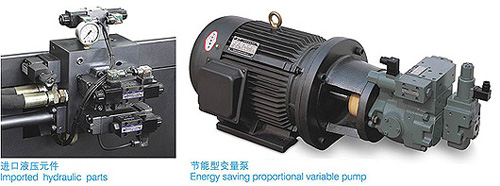
·High precision computer control PLC is combined together
perfectly with high efficiency and energy saving proportion plunger type
variable pump, saves electricity to 25 ﹪ - 50 ﹪, the economic benefits and social benefits are double increased.
At the same time it can lower the oil temperature and less cooling water
consumption and prolong the service life of hydraulic components, reduce the
failure rate, save the maintenance cost.
·High precision returned oil filter can effectively prevent hydraulic oil
pollution and deterioration with effect of NAS - level 7, full flow oil filter.
Therefore, there is no need to change oil, which not only saves the cost for customers
, but also ensures the hydraulic system running more smoothly and the sealing
parts working longer.
·Imported high-grade hydraulic components fitting with differential oil circuit
design guarantee rapid, stable, low noise of the mould clamping. It can shorten
the molding cycle time and improve the production efficiency.
·The oil circuit system is designed with mass flow and plug-in valve , which
not only ensures that the system has rapid response and small impact, but also
reduces the oil pressure loss.
·Spiral guide cooler in high thermal efficiency and low pressure loss ensure
the stable operation of hydraulic system; improve the repetition accuracy and
the product yield.
·The screw is driven by Low speed and high torque hydraulic motor, which can
meet the plasticizing requirements of various raw materials.
Electric
Controller 
·High
performance of switching power supply can normally work with operating voltage
from 160v to 280v , which can be adapted for all kinds of bad power
environment;
·Using high pixel (800 x 480) large capacity TFT true color display, it makes
the display content more rich, the process adjustment more intuitive , the
operating more simple and the function more perfect. It also can simulate
machine action.
·High-speed CPU with increased capacity storage not only meets the requirements
of the process control system, but also can use graphic to record complete
injection process, make the injection process control to be more convenient.
·Large capacity storage make monitoring, alarm, mould parameters store capacity
multiplication, can store 200 sets of mould injection data, can record 200
constitutive monitoring data and 200 times alarm information. Mold data can
choose copy or clear freely. At the same time, it still can use SD card to read
and store the mould data that is more conducive to mass production management.
·Equipped with internet communication port, injection molding machine can be
realized network management, can be real-time monitoring factory production
status and the working condition of injection molding machine, to realize the
factory automation production.
·Perfect automatic monitoring and a large number of internal parameters, can
assist you to adjust machine’s every movement to the best condition.
·Six sections injection speed, pressure and three sections of holding pressure,
speed control, can satisfy all sorts of complex products process conditions.
·Three sections of the charging speed, pressure control, ensure the
plasticizing more uniformity, faster and more stable measurement.
·Rapid temperature control system, using FUZZY control mode, has the faster
warming, high precision characteristics, temperature control accuracy reach to
±1 ℃ in static time.
At the same time it provides high low temperature deviation alarm and
thermocouple bolt check out.
·Function to prevent cold material start-up.
·Mold locking, injection and ejector stroke use high precision electronic
sensor to control the position, the setting accuracy in +/- 0.1 mm.
·Supported with ejector stay, thimble shock and multiple ejector function. the
speed and pressure of thimble forward/backward can be divided into two stage
control.
·Forming number settled with automatic stop, which is more convenient for
production management.
·Defective products monitoring: when machine operates in automatic mode , the
computer will be for each cycle injection monitoring, to judge product and
machine normal or not.
·Automatic Adjustment Mode: can direct input clamping pressure, the mold
thickness will be adjusted by computer automatically, that makes the clamping
force to be in accord with high clamping pressure.
·Data setting lock prevents improper personnel change.
Features of
lubrication system 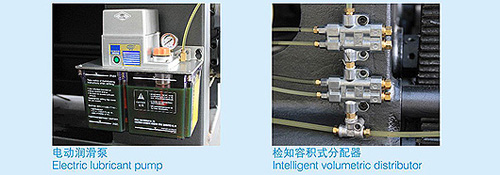
·Major
friction parts are equipped with lubrication points. Central oil supply system
is used for hinges. Electric lubricant pump controlled by computer sends
automatically lubricating oil (grease) to lubrication points. Lubrication is
simple and high efficient.
·Intelligent volumetric centralized lubricating system, controlled by computer,
sends quantitatively lubricating oil (grease) to wearing points, and guarantees
that the key carrying surfaces are lubricated reliably. The repair is visual,
convenient and fast. The service life of the machine is longer.
Standard devices
1 Injection system
. Nitriding alloy steel screw charging barrel
. Standard injection nozzle
. Double cylinder balance injection unit
. Mobile hopper
. Anti-cold start-up of screw
. Automatic dislodging function
. Anti flow casting function
. Multistage charging barrel PID temperature control
(4-7stages)
. Automatic inspection on material molten and material injection fault
. Precision electronic meter control on material injection/molten stroke
2 Mould locking device
. Precision electronic meter control mould locking / thimble travel
. Mould locking three plates / Mould plate & toggle
adopt high rigid nodular cast iron.
. Two stages ejector forward / backward movement controlled by computer
. Mould low pressure protection function
. Hydraulic mould adjusting device
3 .Hydraulic system
. High performance proportional variable pump system
. Molten material back pressure adjusting device
. Full flow precision return oil filter
. Automatic adjustment of system pressure and flow
4 .Control system
. Input / output viewing function
. Setting function of automatic temperature retaining and heating
. Time / position /
pressure, three conversion modes
. Independent adjustment on slope of each movement
. Two-sets of hydraulic core pull / un-screwing mould release
5. Operation manual
. Tool box
. Spare parts
Optional configuration
1 .Injection system
. Long injection nozzle (Extended by25 / 50 / 100mm)
. Special screw & Barrel
. Hopper dryer
. Charging barrel air blowing device
. Injection nozzle protective cover
2 .Mould locking system
. Enlarged mould capacity by 50/100mm
. Super large ejector stroke
. Mould hoisting carrier
. Mould heat insulating plates
. Special mould location ring
. Pneumatic safety door
3 .Hydraulic system
. Hydraulic core pull / un-screwing mould release device
. Hydraulic safety protection
. Independent oil temperature control system
. Sensitive servo injection system
. Closed-loop control variable pump system
. Nitrogen material injection device
. Melt
proportional back pressure control
4 .Control system
. Electric un-screwing mould release device
. Multiple-unit
mold air blowing devices
. Electric rotating mould release dynamic interface
. Change power supply voltage
Note
.Theory injection capacity = screw diameter2×π/4×screw
travel
.Actual injection capacity is the maximal weight of polystyrene (
PS ) raw material injected to air.
.When UPVC, PC, PMMA, PA and other engineering plastic material
are used, please let us know. When you need modifying parameters and functions
of the machine, please let us know also.
.According to demand of machine upgrade, we will change technical
parameters, configuration of some parts and service’s items without prior
notice.
.Photos are for reference only. If there is any difference with
actual products purchased, the real products are final.
.In normal condition six months warrantee for barrel & screw;
but using caustic or any recycling material is not guaranteed.
Parameter
Type
|
HD10000-8350
|
HD6800-5427
|
HD3300-1902
|
HD4000-2499
|
HD900-300
|
HD5000-3514
|
CLAMPING UNIT
|
T-shot platen
|
|
|
|
|
|
Clamping
force, KN
|
10000
|
6800
|
3300
|
4000
|
900
|
5000
|
Opening
Stroke, mm
|
1150
|
930
|
600
|
710
|
320
|
830
|
Max. daylight,
mm
|
2300
|
1870
|
1300
|
1400
|
680
|
1680
|
Platen Size,
mm*mm
|
1700*1700
|
1340*1340
|
985*985
|
1050*1050
|
540*540
|
1260*1260
|
Space between
bars, mm*mm
|
1160*1160
|
930*930
|
670*670
|
740*720
|
360*360
|
820*780
|
Max. mold
height, mm
|
1150
|
940
|
700
|
730
|
360
|
850
|
Min. mold
height, mm
|
500
|
350
|
300
|
300
|
130
|
300
|
Ejector
stroke, mm
|
350
|
265
|
180
|
210
|
100
|
220
|
Ejector force,
KN
|
290
|
184
|
77
|
110
|
34
|
135
|
INJECTION UNIT
|
|
|
|
|
|
|
Screw
diameter, mm
|
100 110 120
|
83 90 83
|
60 68 75
|
68 75 83 90
|
30 36 42
|
75 83 90 100
|
Screw L/D
ratio,
|
23 21 19
|
23.5 21 19
|
21 21 19
|
21 20 17.6
17.5
|
20 20 17
|
23.8 21 19.9
17.8
|
Injection
Pressure, Mpa
|
205 169 142
|
223 190 154
|
217 169 139
|
208 171 140
119
|
266 185 136
|
204 167 142
115
|
Shot volume,
cm3
|
4084 4942 5881
|
2435 2863 3534
|
876 1126 1370
|
1198 1458 1786
2099
|
113 163 222
|
1722 2110 2481
3063
|
Shot weight
(ps), g/OZ
|
3838/135
4644/164 5527/195
|
2288/81
2690/95 3321/117.6
|
823/29
1058/37.3 1287/45.4
|
1126/39.7
1370/48.3 1678/59 1973/70
|
106/3.7
153/5.4 208/7.2
|
1619/57.1
1983/70 2332/82.3 2879/101.5
|
Injection
rate, g/sec
|
686 830 988
|
400 470 581
|
238 306 372
|
283 344 421
495
|
54 78 106
|
358 439 516
637
|
Plasticizing
Capacity, g/sec
|
85 106 121
|
69 86 94
|
57 67 81
|
58 70 80 88
|
13 19 26
|
68 80 88 94
|
Screw stroke,
mm
|
520
|
450
|
310
|
330
|
160
|
390
|
Screw speed,
rpm
|
115
|
135
|
174
|
122
|
184
|
133
|
POWER UNIT
|
|
|
|
|
|
|
Hydraulic
system pressure, Mpa
|
17.5
|
17.5
|
17.5
|
17.5
|
17.5
|
17.5
|
Pump motor
power, kw
|
55+37
|
55
|
30
|
37
|
11
|
45
|
Heater power,
kw
|
42
|
38
|
18
|
22
|
6
|
28
|
GENERAL
|
|
|
|
|
|
|
Dry circle
time, sec
|
|
|
3.2
|
4
|
1.5
|
5.8
|
Oil tank
capacity, L
|
1600
|
1000
|
460
|
630
|
180
|
810
|
Machine
weight, kg
|
50
|
32
|
10.8
|
15
|
2.8
|
18.5
|
Dimension
(LxWxH)
|
11.0*2.9*3.1
|
9.1*2.4*2.5
|
6.8*1.62*2.3
|
7.2*1.65*2.3
|
3.8*1.1*1.7
|
8.7*2.1*2.3
|
|